Sheet metal machining is a popular type of mechanical fabrication today. 83MEC is equipped with modern production lines and automated stamping technology by specialized machines for efficient sheet metal processing, significantly cutting and bending and stamping machines. As a result, sheet metal processing products have high accuracy and aesthetics. 83MEC has mastered sheet metal processing technology with various products supplied to the market and exported to the world, typically Ammo Metal Box products. Therefore, 83MEC wants to share with our customers how we master sheet metal processing.
I. Sheet metal processing methods applied at 83MEC
– Sheet metal processing by traditional techniques such as planing, grinding, turning, and reaming can only meet some of the strict requirements in today’s medium and large-scale automated and mass production lines. 83MEC will have to combine many processes with varying complexity and requirements for finishing sheet metal. However, those processes revolve around the following typical processes:
+ Cut
+ Bending metal
+ Metal punching
+ Stamping claws
+ Welding
+ Surface treatment
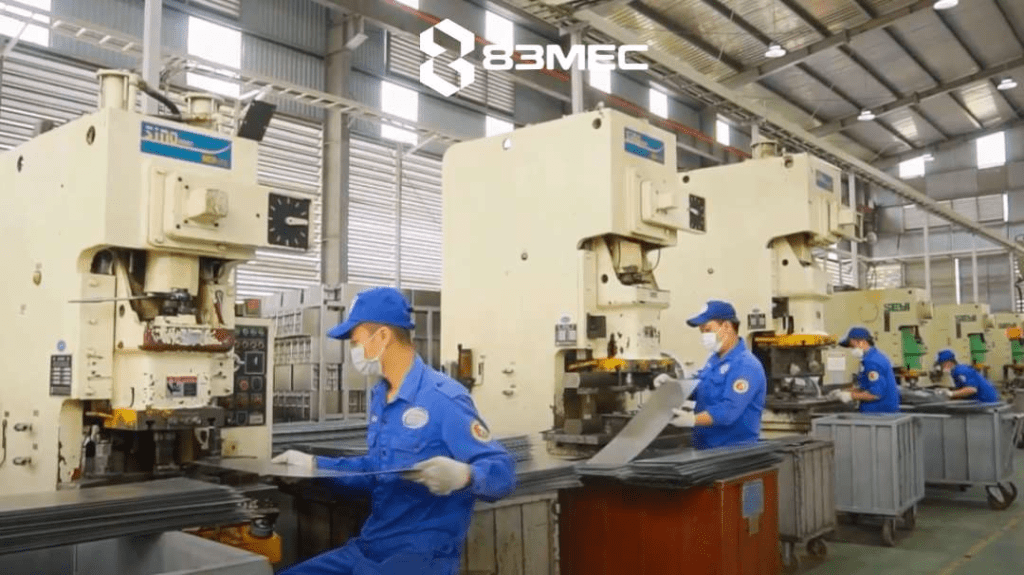
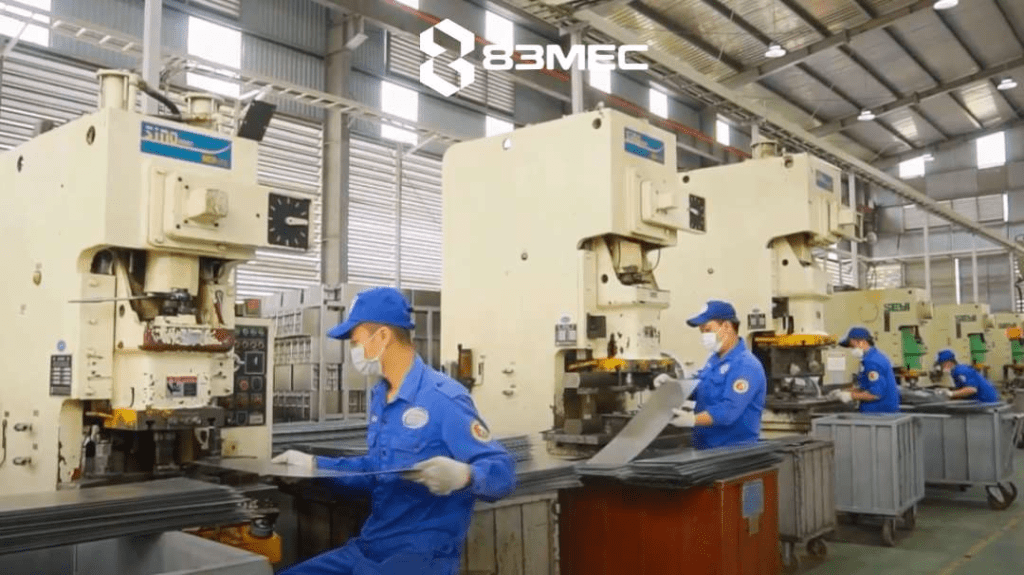
1. Metal cutting method
Metal cutting methods can be divided into 4 main groups of methods:
– A blade with high hardness can only cut relatively soft metals, easy to manipulate, such as copper, aluminum, and specialized steel for cutting. This is a simple method and does not require high equipment and tools. However, it has the disadvantages of time-consuming, complicated machining, low safety and accuracy.
– Cutting technology with Gas or Acetylene torch: usually applied to cut metals with a thickness of over 30mm. This method has the advantage of cost, cutting thick details, but the accuracy is low, depending on the skill of the craftsman.
– Plasma cutting technology: Based on taking advantage of high temperature and high transmission speed of gasses, Plasma technology uses gasses capable of conducting electricity when supplied with a large enough energy source. The strong oxidation process and the continuous current from the ionization of the gas atoms will create a plasma current. During the cutting process, a hot amount of plasma gas is used to melt the material and make a precise cut that pushes the metal materials off the cutting surface. This technology is commonly used in industrial applications such as cutting steel, aluminum and copper. Plasma-cutting technology has many advantages, such as fast cutting speed, cutting thick materials, and cutting diverse materials.
– Laser cutting technology: Laser cutting technology in cutting machining is a method that uses a laser to cut or punch holes into various materials such as metal, wood, plastic and non-conductive materials. This technology provides precision with high cutting speeds while minimizing errors compared to traditional cutting methods. Using laser cutting technology in machining increases productivity, reduces production time and costs, and provides high-quality products that meet the increasing market demands.
2. Metal Bending
– There are two common sheet metal forming methods: folding and metal bending. The shape of the workpiece will be deformed to create products of different shapes. Currently, the processing workshops will use CNC bending machines to shape the correct size and bend the angle as required with a tolerance of up to +-0.5mm.
3. Metal punching
– Metal punching turns flat metal sheets into specific pattern shapes based on punching or cutting out excess material. The punching and stamping techniques used to shape metal can be mentioned as punching, bending, casting, embossing, etc.,
– The punching mold plays a vital role in this operation; it determines the quality of the product being punched. Each different product needs to be designed and manufactured with different types of molds, the following is a group of commonly used molds today:
+ Simple stamping mold: this is a type of mold that definitively performs one operation per stamping, but the operation is long and reduces flexibility. Suitable for single products.
+ Combination mold: This is the type of mold where the punched parts are completed after one press of the machine. All punching operations to form the product are performed at the same time. The stamping process is complete and a finished product emerges from the mold. This is a flexible method, highly applicable, saving time and human resources.
+ Continuous punching mold: A continuous punching mold is a tool used in mechanical processing to produce metal parts in large quantities and with high precision. Continuous punching mold designed for punching and bending metal sheets into products with complex shapes. Continuous stamping dies are commonly used to produce metal parts for automotive, electronics, refrigeration, home appliances and many other industries. Straight stamping dies can be adapted to produce products of different sizes and shapes and are often used in mass-production processes to reduce costs and increase productivity.
4. Metal welding
Welding is the process of joining fixed parts together after cutting, bending or punching steps to form a finished product by applying high temperature and pressure to the joints.
Currently, there are three main welding methods, including butt welding, spot welding and line welding.
– Spot welding is the most common form of electric contact welding, in which the welded parts are pressed on top of each other, welded on each point, and usually applied to thin metal sheets.
– Line welding: used to weld metal pieces with a total thickness of less than 4mm. This method differs from spot welding in that the roller electrodes replace the rod electrodes. When the roller rotates, the solder is between the 2 rollers. Therefore, the weld is a very tight line that does not allow liquids and gasses to pass through.
– Butt welding: welded parts are together on their entire contact surface. This method includes two sub-methods: resistance welding (no melting) and fusion welding.
5. Surface treatment
– Surface treatment and product finishing, including methods that can change the surface properties of metal workpieces. Each surface technology process will help the product to be optimized in terms of quality and aesthetics. It must also meet the requirements for:
+ Insulation ability (diffusion, penetration, anti-corrosion)
+Surface mechanical protection. Anti-friction, wear-resistant.
+ Increased optical function (absorption, reflection, decoration)
+ Add insulation or conductive function.
– The operation is performed through standard machining methods such as:
+ Surface removal (polishing method).
+ Surface coating processing: paint, powder coating, nickel coating, chromium coating, zinc plating, aluminum anode, black dyeing, …
+ Mechanical surface treatments include shot peening, flat grinding, and chamfering.
+ Chemical surface treatment, including cleaning and cleaning.
The manufacturing methods of sheet metal mentioned above will contribute to the diversity and high aesthetics of the product. Make metalworking products of higher quality and use value. Each operation has different independent roles and tasks. However, to make a complete sheet metal product, combining many of the above operations is necessary.
In sheet metal machining, 83MEC has applied various methods to flexibly meet customers’ processing needs. With the investment in modern machinery and equipment, optimizing production productivity has helped 83MEC create specific products of this technology and supply products of outstanding quality to the market, typically such as ammo metal box, and grills,… are exported to the US and European countries with high turnover. Come to 83MEC if you need to process high-quality products from sheet metal with the most competitive cost in the market. For more information, don’t hesitate to contact info@83mec.com for quick support.