Deep drawing stamping is a mechanical processing method used to shape products by pressing thick metal sheets into complex shapes, such as parts for automobiles, motorcycles, and industrial machinery. In increasingly fierce competition, businesses must find solutions to optimize production processes, increase productivity and reduce costs. Deep drawing stamping is an optimal solution for manufacturing companies while optimizing production to produce high-quality products at a reasonable price. In this article, 83MEC will explore why deep drawing is the optimal solution for mechanical machining.
1. What is the process of deep drawing?
Deep drawing (in the context of sheet metal forming) is the process by which a flat sheet of steel is transformed into a deep (often complex) shape, in which the flat sheet is “drawn in” from the edges and “sucked in” to create a deep shape that would not be possible using conventional metal forming techniques.
Deep drawing technology is used in many industries, including manufacturing automobiles, home appliances, medical equipment and other industrial products. With this technique, parts can be produced in large quantities and with high precision, which increases production productivity and reduces production costs.
2. Advantages and disadvantages of the deep drawing stamping method
The deep drawing stamping method offers several advantages and disadvantages. Let’s explore them:
2.1 Advantages of Deep Drawing Stamping
- Cost-effective: Deep drawing can be a cost-effective manufacturing method, as it allows for producing complex shapes from a single metal sheet. This reduces the need for additional fabrication processes and assembly.
- Material Efficiency: Deep drawing utilizes the material efficiently, minimizing scrap and waste. The process involves stretching and redistributing the material rather than removing excess material through cutting or machining.
- Strong and Durable Products: Deep drawing results in high strength and structural integrity components. The uniform distribution of the material in the formed shape enhances the strength and durability of the final product.
- Versatility: Deep drawing can be used with a wide range of sheet metal materials, including stainless steel, aluminium, and brass. This versatility allows for the production of various products across various industries.
- Mass Production Capability: Deep drawing can be easily automated and integrated into high-volume production lines. This makes it suitable for mass production, resulting in faster production cycles and increased efficiency.
2.2 Disadvantages of Deep Drawing Stamping
- Design Limitations: Deep drawing has certain design limitations due to the nature of the process. It is more suitable for symmetrical shapes and parts with uniform thickness. Complex conditions with varying wall thicknesses may require additional manufacturing steps or alternative methods.
- Tooling Costs: The initial tooling costs for deep drawing can be relatively high. Dies and punches must be designed and manufactured for each product, which may involve significant upfront expenses.
- Material Stretching and Thinning: During the deep drawing process, the material undergoes stretching, which can lead to thinning in certain areas. This thinning may affect the component’s structural integrity, requiring careful design considerations.
- Limited Depth-to-Diameter Ratio: Deep drawing limits the depth-to-diameter ratio that can be achieved. As the depth increases, the chances of wrinkling, tearing, or material flow issues may arise, necessitating additional forming steps or alternative processes.
- Surface Imperfections: Deep drawing can result in surface imperfections such as wrinkles or distortions. Proper lubrication, blank holding, and tooling design are essential to minimize these issues.
It’s essential to evaluate these advantages and disadvantages in the context of specific manufacturing requirements and product design considerations to determine the suitability of deep drawing stamping for a particular application.
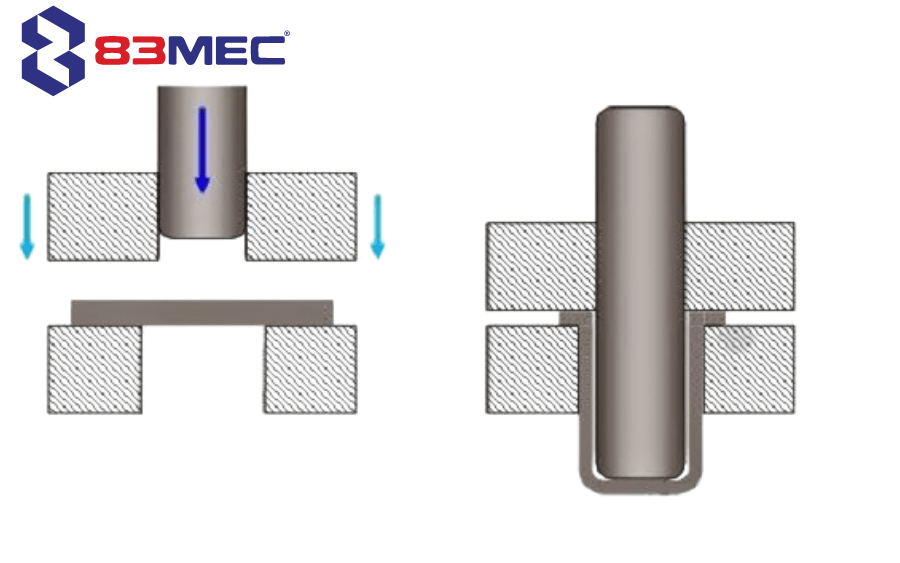
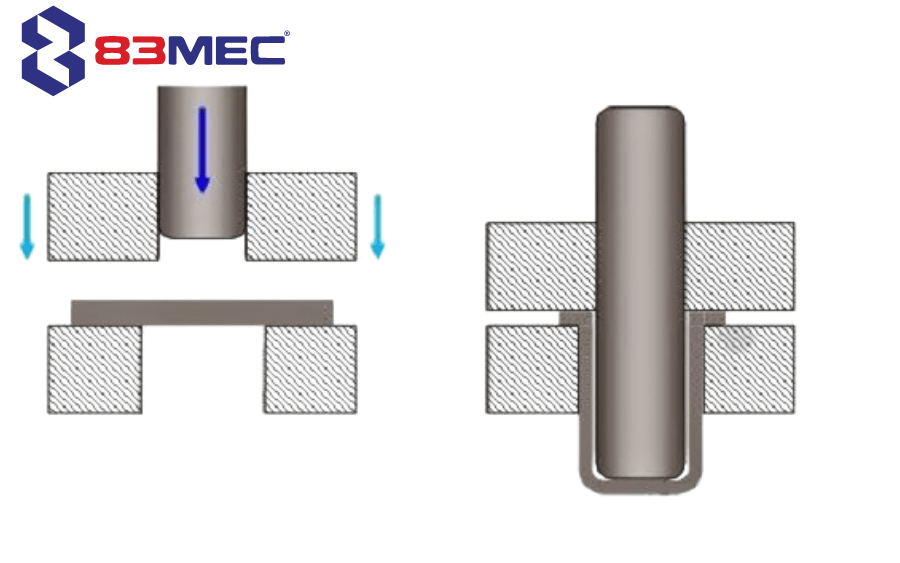
Deep Drawing
3. How is deep drawing stamping applied in mechanical production?
Deep drawing stamping is widely applied in mechanical products to manufacture various components and products. Here are some typical applications of deep drawing stamping in mechanical production:
- Automotive Industry: Deep drawing is extensively used in the automotive industry for producing components such as car body panels, fuel tanks, exhaust systems, and engine parts. The ability to create complex shapes and seamless structures makes deep drawing an ideal choice for automotive manufacturing.
- Appliance Manufacturing: Deep drawing produces household appliances like washing machine drums, refrigerator components, and oven cavities. The process allows for the creation of precise and durable parts with excellent fit and finish.
- Aerospace and Aviation: Deep drawing is utilized in the aerospace and aviation industries for manufacturing aircraft parts and components, including fuel tanks, engine housings, and structural elements. Deep-drawn parts’ lightweight yet strong characteristics make them suitable for aerospace applications.
- Electronics and Electrical Equipment: Deep drawing is employed in producing electronic enclosures, connectors, and various electrical components. The process ensures the creation of intricate shapes with precise tolerances, providing protection and functionality for electronic devices.
- Medical and Healthcare: Deep drawing manufactures medical devices and equipment such as surgical instruments, implants, and containers. The medical field’s ability to produce complex and sterile components with high precision is crucial.
- Industrial Machinery: Deep drawing is applied in producing machinery and equipment, including hydraulic cylinders, pressure vessels, and industrial tooling. The process enables the creation of solid and reliable components essential for industrial operations.
Deep drawing stamping is favoured in mechanical production due to its ability to create complex shapes, high production efficiency, material utilization, and cost-effectiveness. It plays a significant role in various industries, enabling the production of quality components that meet specific design and functional requirements.
Deep drawing stamping technology at 83MEC is equipped with a system of specialized and advanced machines operated by a team of experienced and highly specialized technicians to ensure product quality meets the standards required by customers. If you need mechanical processing services using deep drawing technology, please get in touch with 83MEC for advice and provide the optimal solution for your needs.