Metal forging is a fundamental process in the manufacture of metal parts. With the development of technology, the metal forging process at 83MEC is realized by combining experience and modern technology. With the application of advanced technologies, the metal forging process at 83MEC brings quality products and meets customers’ requirements. Let’s learn more about the metal forging process at 83MEC in the article below.
1. Overview of forging technology
1.1 What is the essence of forging technology?
Forging is a processing method that has been applied for a long time; the development of technology has improved the forging process with modern and specialized machines and equipment to support traditional forging methods, thereby achieving higher production efficiency, ensuring in terms of quantity and quality. The essence of the forging process is to use external forces applied to ductile materials to change the workpiece with the required shape and size.
Currently, there are two main forging methods: free forging and Impression-die forging (closed-die forging). Different forging methods are flexibly applied based on the product’s characteristics to be processed. As follows:
– Free forging is the process of processing metal under the action of external force through a hand hammer or machine hammer to deform the workpiece. The workpiece is heated to a specific temperature to convert the metal billet into a plastic state, and then an external force is used to change the shape of the workpiece as required.
– Impression-die forging (closed-die forging) is a machining process that deforms the metal inside the mold. Under the stamping force of the device, the metal is deformed in the mold cavity.
* Features of the free forging method:
– Machining parts have low precision, and surface gloss is low.
– It is difficult to be consistent in each part’s quality and metal properties, so it is only suitable for processing simple parts, small quantities or complex non-shaped surfaces.
– Long processing time, low productivity
– The quality of the product depends mainly on the workers’ skills.
* Compared with free forging, impression-die forging has the following characteristics:
– Impression-die forging provides higher forging accuracy and quality than free forging.
– Capable of machining complex parts.
– High productivity
– Easy to mechanize and automate.
– However, the high cost of mold-making makes the forging method suitable for mass production.
2. What metal forging methods does 83MEC have?
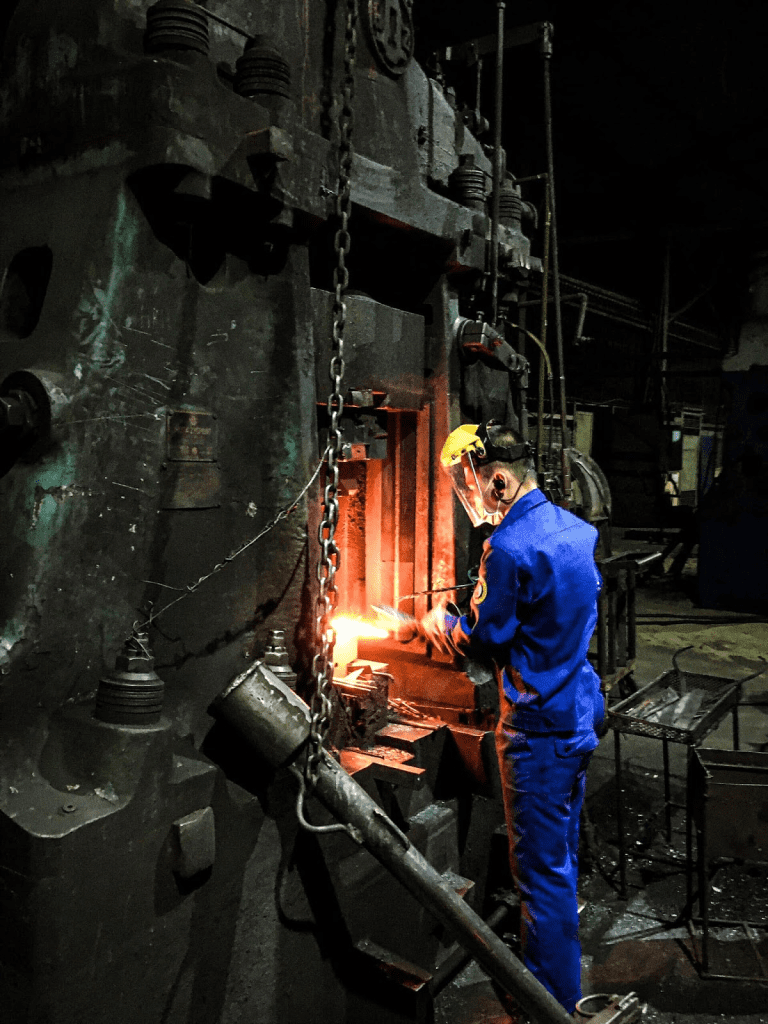
2.1 Free forging
- Free forging at 83MEC is applied to forging parts with simple profiles, suitable for small-order production, and single production.
- Necessary tools used by 83MEC in free-forging
- Basic tools include an anvil, hammer, tongs, spade, and awl.
- Clamping tools such as pliers, vices and other clamping devices.
- Testing and measuring instruments: eke, calipers (inner gauge, depth gauge, the compass of all kinds.
2.2 Impression-die forging (closed-die forging)
The forging method is applied by 83MEC to process and create billets of complex shapes for products such as pliers, electrical accessories, and water industry accessories.
The leading equipment used in closed-die forging includes:
- Heating equipment, conveying equipment, billet cutting machine, cooling equipment, testing equipment,…
- Large capacity stamping machine.
- Air hammer, crankshaft compressor, hydraulic press, friction screw press,…
3. System of machinery and equipment for metal forging at 83MEC.
For 83MEC to provide its customers with quality forging products at competitive costs, it is indispensable to equip themselves with various modern machines to bring high productivity and economic efficiency. We always strive to meet the machining needs of our customers fully. Notable machines and equipment include:
- Hammer machine 250 kg
- Steam Hammer 1.5T
- Hammer machine 150 kg
- Hydraulic hammer forging machine.
- Sand blasting machine
- Shot blasting machine
- Induction medium frequency furnace 1500C
- Frequency furnace (Electrical cabinet, induction loop, cooling system)
- Medium-frequency heating furnace.
In this article, we learned about metal forging technology at 83MEC – a manufacturing technology that has been applied and developed over the years. Through the combination of experience and modern technology, 83MEC has been and continues to meet the production needs of domestic and foreign customers. Products using 83MEC forging technology are created with high precision and meet quality standards according to the customer’s processing requirements. Come to 83MEC for support and advice on the best production solutions when you require metal machining.